Amid the current market of record-high container freight rates and widespread equipment shortages, which are likely temporary despite the pain inflicted on shippers, there are signs of a longer-term change in the market where more shippers are gaining an appetite for premium services, pushing the industry away from commoditization and toward value creation.
There is a difference between surcharges linked to real-time market conditions, the somewhat longer horizon of contract pricing terms, and actual underlying changes in how business is changing that would represent potentially permanent change in the market. Despite all the noise around the current lofty spot rate market, more subtle, but important, changes are sneaking into the market that provide guidance on where things may be headed in coming years.
Premium services are a good place to start. In the decade that has followed the financial crisis, which was characterized by overcapacity, commodity pricing, and lack of service differentiation, carriers’ efforts to introduce value-creating services were, for the most part, non-starters. One example was Daily Maersk, launched in 2011 and suspended in 2015, under which the world’s largest carrier sought to create a conveyor belt of daily sailings out of China with a premise of guaranteed delivery times for which it sought to extract a premium rate. In the environment of that time, that wasn’t possible.“Daily Maersk is a premium product in terms of reliability and frequency, but there has not been a big demand to pay the premium it takes to run the service," Maersk said at the time.
Another example was the Ocean 53 product APL debuted in 2007, which gave shippers with cargo headed from Asia into interior North America access to a container with 60 percent greater carrying capacity than a standard 40-foot box, reduced handling costs, and faster transit times. Apparel shippers were especially keen on the idea, but there was not enough demand for APL to command a premium price. In other words, efforts by carriers to introduce, and be paid for, value-added services in prior years would typically disappear in the dual undertow of overcapacity and the absence of rate discipline.
Premium services gaining foothold amid COVID impact
But in a development not directly related to the current frothy freight rate market, premium services have begun to reappear and, unlike in the prior era, are slowly and unceremoniously gaining a foothold and will get a push from the COVID impact on the supply chain. Reflecting that demand, Matson on Oct. 14 confirmed it would make its second expedited trans-Pacific service permanent. Driven in large part by growing supply chain demands of e-commerce, CMA CGM in 2018 and Zim Integrated Shipping Services this year joined Matson in offering expedited trans-Pacific services.
The CMA CGM EEX service has a transit time to Southern California of 11 days from Shanghai and 12 days from Ningbo, two days faster than typical trans-Pacific transit times. CMA CGM is offering further enhancements in the form of guaranteed loading, priority offloading and handoff to trucks, and rapid transfers to rail. As these services gain traction, it will illuminate something profound in container shipping: whether carriers will be able to secure differentiated pricing based on differentiated service. If they are successful, that would be a new evolution with a potentially massive long-term impact. There is even talk of shippers with inconsistent or seasonal volumes paying to ensure erratic weekly volumes get loaded.
In the past, “quality of service was so compressed between the carriers that there’s little differentiation between the top and the bottom. Now you're starting to see that accordion move back a little bit, and you're starting to see the higher end carriers get to a point where they can command a premium,” said James Caradonna, general manager pricing/Americas at M&R Forwarding and Multi Container Line. “Now, initially it's through these premium services, but in our view, the premium services are allowing the market to move toward a new norm. I believe that there's certainly going to be the reestablishment of service tiers among the carriers.” A change such as that is of a different nature than short-term rate volatility or surcharges that are imposed or implemented due to current market conditions. According to Caradonna, a number of carriers have taken advantage of market conditions to pull back on free-time provisions while at the same time making upward adjustments to their respective per diem tariffs. One carrier even imposed an equipment repair fee that Caradonna says “is not something that would have come about during ‘normal’ circumstances.”
The conditions seen in 2020 are likely to carry over into trans-Pacific contract negotiations next year, where the terms and conditions discussed would also be a product of current circumstances. For example, some carriers expect that after a year in which space and equipment were in limited supply, shippers will demand that guarantees be incorporated into contracts, similar to what they did after 2010, when tightness was magnified by the post-financial crisis restocking. But even ensuring space and equipment is a growing priority that is not entirely tied to the experience of 2020. The growth of the New York Shipping Exchange (NYSHEX), which is based on the principle of mutual commitment in ocean contracts, shows how reliability and the costs associated with it are increasingly important to shippers. That is likely to continue long after the disruption seen in 2020.
Drayage shortage crimps supply chain amid quick demand recovery
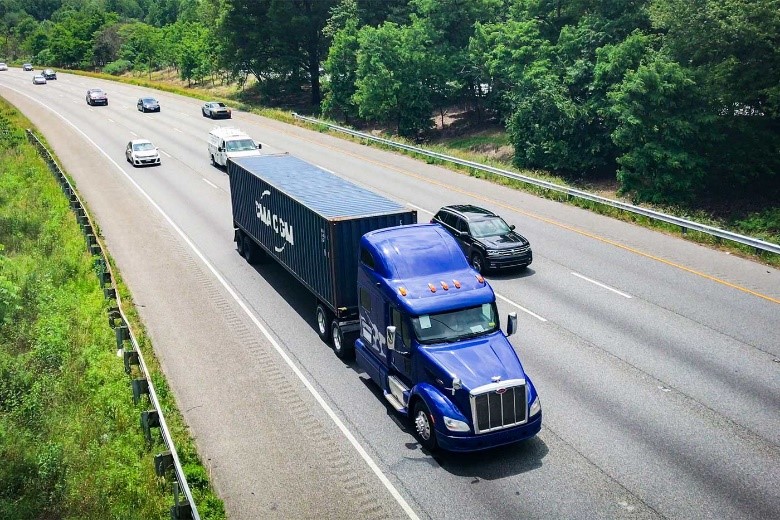
The amount of available drayage capacity in the market to handle container movements has dwindled in recent months due to a combination of factors. Those include a quick rebound in volume at ports and inland rail terminals, a slowdown in shippers unloading and returning containers, and drivers exiting the industry during the COVID-19 pandemic.
The rapid swing in volumes has exacerbated the capacity shortage, as ports and railroads suffered double-digit declines year over year in the second quarter, only to see a quick return to year-over-year growth in the third quarter, according to intermodal marketing and trucking executives.
The supply chain is unaccustomed to such whiplash-like change, according to these executives, which has caused equipment and truck availability to become a problem.
“We find that capacity is limited and most dray carriers are booked out two or three days in advance,” said Jon Krystek, chief operating officer for Knichel Logistics. “The 53-foot drayage market right now is very challenging. Our recovery has plateaued, but it has not been due to the lack of demand, it’s the lack of drivers and equipment.”
Laden imports to the Port of Los Angeles declined nearly 15 percent year over year between February and July, but have risen 22 percent year over year in August and September combined, according to PIERS, a sister product of JOC.com within IHS Markit. The port of Savannah saw laden imports fall 23 percent between March and July, but they have risen 8.9 percent in August and September year over year, according to PIERS. Savannah and other East Coast ports began to feel the impacts of Chinese factories shutting down due to the COVID-19 pandemic a month later than the West Coast due to the longer transit times.
Domestic volume grew 9.8 percent year over year in the third quarter, setting a new third quarter intermodal record with 2.4 million units moved, according to the Intermodal Association of North America. While international intermodal fell 6.5 percent year over year in the third quarter, last month's international rail volume was up nearly 3 percent over September 2019. Domestic volume surged 14.6 percent year over year in September.
CSX Transportation and Union Pacific Railroad illustrate the rapid shifts in volume on the rails. CSX had the weakest second quarter since 2011, while UP had its lowest volume since the Great Recession of 2008-09. In the third quarter, however, both railroads saw volume rise more than 6 percent year over year and grow 20 percent compared with the second quarter, according to the Association of American Railroads.
Ken Kellaway, CEO of drayage provider RoadOne IntermodaLogistics, said it takes time to react to rapid swings in volumes. “Import volumes into West Coast ports doubled over a one- to two-month period and the drayage capacity and chassis are not available to react to this large of a surge,” he told JOC.com. “This same impact has been felt in most major import and rail intermodal markets nationwide, but to a lesser degree since West Coast ports are the closest access point to Asia. We anticipate this capacity challenge will exist for the next two to three months.”
“The system needs to adjust to the surge and the shipper and the consignee can help with flexibility — that is a big missing link,” added Sam Farruggio, owner of drayage provider Farruggio’s Express.
Finding drivers is a problem
When volume was at a low in the spring, trucking executives said they lost many drivers. Instead of riding out the downturn, they said older drivers decided to retire or take different jobs.
“Demand is extremely high and since most carriers had cut back on hiring earlier this year and fewer new drivers have entered the market, a perfect storm has been created,” said Ben Banks, vice president of drayage provider TCW Inc.
Kellaway said a great deal of drayage capacity left during the pandemic and it’s been hard to find new drivers.
“Many of these drivers have not returned, and have elected to go to other industries or other sectors such as truckload, which is paying a very high premium at the present time due to capacity shortages,” he said. Dry van spot market rates have risen to levels even higher than in 2018 with a surge in e-commerce shopping and increase in purchases of durable goods such as furniture, appliances, and other home improvement items. Drivers who complained this spring about unsustainable pay on spot loads are now earning some of the highest per-mile rates in history.
Terminal congestion and slow unloading
Farruggio notes that driver productivity is also a real problem. Drivers are completing fewer deliveries per day and therefore more trucks are necessary to handle the same volume as in the past.
“The Northeast markets are all short of drivers and the demand exceeds the workforce, the lack of efficient use of the supply of drivers is the real problem,” he said.
It’s an issue J.B. Hunt Transportation Service noted as a core problem in its intermodal results released Oct. 16.
“Rail terminal congestion and a slower pace of unloading at customer destinations have contributed to a meaningful slowdown in the velocity of the supply chain and thus the productivity of our equipment,” Darren Field, J.B. Hunt’s executive vice president of intermodal, said on the company’s earnings call.
Containers and chassis
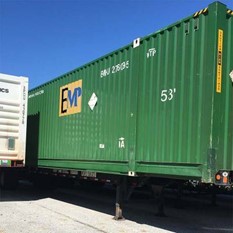
Photo credit: Ari Ashe.
Field said J.B. Hunt had to turn down business because there weren’t enough available containers to support new opportunities. The container problem has also been a problem on UP’s rail network this summer with rail-owned UMAX and EMP containers. Intermodal logistics executives have told JOC.com that less than 20 percent of requests for UMAX and EMP containers are being granted in California.
“Some weeks along the way have been a bit better, but to be honest there is no significant improvement since July,” Krystek said.
Chassis issues have popped up on both international and domestic containers, the trucking executives said. Available TRAC Intermodal chassis were running low in Columbus in recent weeks, and TCW’s Banks said availability is also tight in Memphis.
Farruggio said the bigger problem is on the domestic side.
“The international side has done a great job with chassis supply and quality,” he said. “The domestic, 53-foot world has fallen short on supply and quality. Many days we find units on the ground due to no chassis or placed on a bad chassis.”
That’s unusual because J.B. Hunt, Schneider National, and XPO Logistics have their own chassis, and Hub Group and EMP containers are stacked on Norfolk Southern chassis in the East. But it shows just how tight equipment is in the US right now.
Chassis shortage in LA–LB likely to persist into 2021
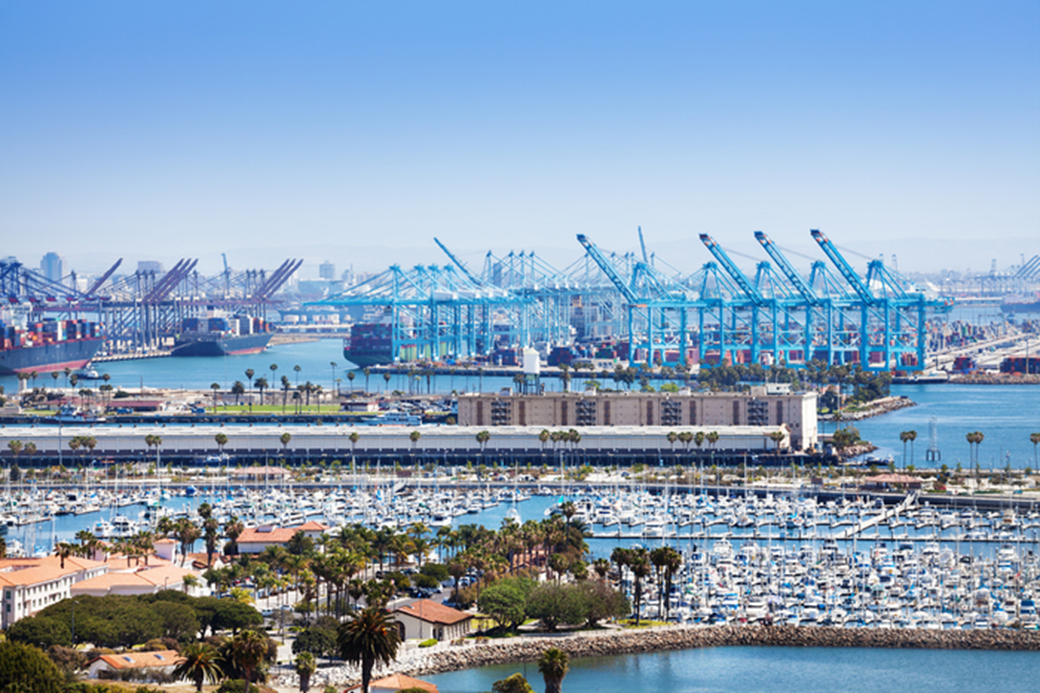
Intermodal equipment providers (IEPs) say while they are making an all-out effort to remedy chassis shortages in Southern California, the shortages will likely persist into next year if the ports of Los Angeles and Long Beach continue to handle record import volumes from Asia.
IEPs and truckers blame inefficiencies at marine terminal gates as a major cause of the chassis shortages, and want the ports to require that ocean carriers share advance shipment information that will increase cargo velocity throughout the supply chain.
The IEPs note that pushing record container volumes through the Southern California supply chain over the past three months has stretched the assets and manpower of marine terminals, truckers, railroads, and distribution warehouses beyond capacity. They say it is unfair to single out chassis providers as the weakest link in the chain, especially because the IEPs are taking charge of those issues over which they have control, such as repairing out-of-service chassis. “We are maxed out on fixing bad-order chassis. Our mechanics are working flat out. We couldn’t employ one more mechanic,” said Ron Widdows, CEO of Flexi-Van Leasing. DCLI, TRAC Intermodal, and Flexi-Van operate the Pool of Pools through which the three IEPs manage the fleet of interoperable chassis in Southern California.
Truckers, meanwhile, say the issues that contribute to inefficiencies in the Southern California supply chain have been well known for years and did not suddenly emerge because imports from Asia recovered faster than anticipated this summer. Weston LaBar, CEO of the Harbor Trucking Association (HTA), said the ports’ main failing is they are not doing enough to bring ocean carriers to the table with solutions that will enhance cargo velocity.
“I am sick and tired of the lack of action,” he told JOC.com Wednesday. “What do they mean, ‘There is too much cargo’? This is what we all do. We move cargo.”
The HTA has called upon port authorities to incentivize — and, if necessary, compel — ocean carriers to share shipment information with other members of the supply chain, so all asset owners are prepared for the cargo volumes they will be handling. In the case of truckers, who suffer the brunt of the delays at marine terminals, the key is for carriers to provide them with reliable shipment information so they can arrange appointments that foster dual transactions, LaBar said.
Dual transactions, which involve hauling an export load or empty container to the terminal and taking delivery of an import load on the same trip, can greatly increase trucker productivity, but dual transactions only account for about 20 percent of trucker visits to the harbor, LaBar said.
“Dual transactions, dual transactions, dual transactions. That’s the solution,” he said.
Import spike expected to continue through January
Shipments of personal protective equipment, e-commerce merchandise, and home improvement goods have been strong since late June as the US economy reopened from initial COVID-19 lockdowns. Imports are expected to continue at a high level until factories in Asia shut down for the annual Lunar New Year holiday beginning Feb. 12, 2021.
The Los Angeles-Long Beach port complex in September handled 828,880 TEU of imports from Asia, up 22 percent from September 2019, according to PIERS, a JOC.com sister company within IHS Markit. In the four-month period from June through September, imports from Asia moving through the largest US container gateway totaled 3.09 million TEU, up 12 percent from the same period last year.
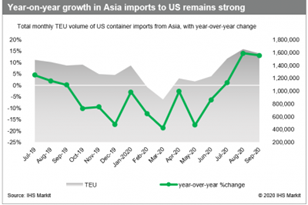
Click to enlarge.
The three IEPs that operate the Pool of Pools in Southern California say they are doing everything they can to expand the chassis pool, which totals about 65,000 units, including purchasing new chassis, repositioning chassis from surplus locations in other parts of the country, and working overtime to repair damaged chassis that are not roadable.
Daily updates on the Pool of Pools website show the IEPs have made great strides in recent months in repairing out-of-service chassis. Some 4,246 units were out of service at the 12 container terminals and four intermodal rail ramps in Southern California as of Wednesday, down from more than 8,000 bad-order chassis in June.
“Our contribution to the Pool of Pools is up,” said Ron Joseph, executive vice president and COO of DCLI. He said DCLI is also repositioning chassis from surplus locations in the Midwest.
Widdows said Flexi-Van’s contributions to the pool actually exceed its original commitment. Flexi-Van in September began deploying the first of 1,500 new-order chassis into its Southern California fleet. “We will continue to acquire new chassis through the end of this year and into next year,” he said.
TRAC Intermodal has new chassis on order, but due to tariff issues between the US and China, the IEP had to shift its purchases to North American suppliers, which delayed the orders, according to Val Noel, executive vice president and COO. The new chassis will begin to arrive in the second quarter of 2021, he said.
Productivity down throughout the supply chain
Port stakeholders have struggled with supply chain challenges all summer and fall. The problems began when distribution warehouses became filled to capacity due to a shortage of workers as COVID-19 cases spiked this summer. Warehouse operators also had to spread workers out at their facilities for safety purposes, which contributed to a decline in productivity.
As a result, the average container/chassis “street dwell” time more than doubled from about 3 days earlier this summer to 7.1 days this week, according to the Pool of Pools website. The average container dwell time at Los Angeles and Long Beach marine terminals rose to 3.25 days from 2.8 days in July, according to the Pacific Merchant Shipping Association, while the average truck turn time in September was 77 minutes, up from a record-low 58 minutes in June, according to the HTA’s truck mobility data.
Chassis shortages have also emerged at rail ramps. Union Pacific’s Intermodal Container Transfer Facility (ICTF), located about five miles from the harbor, has recently begun to ground containers because the Pool of Pools chassis supply tightened, UP spokesperson Raquel Espinoza said. Truckers say that is adding time to their ICTF visits compared with the normal process of taking delivery of containers that have been pre-mounted on chassis.
“We are working cooperatively with truckers to identify and mount stacked containers, but there are some delays since that process is outside of normal operations,” Espinoza said.
Crystal ball hazy
The IEPs are developing their business plans for 2021, but are struggling to project how COVID-19 will affect consumer demand, economic growth, and retailers’ strategies for inventory replenishment and storage, Widdows said.
“What Q2 next near will look like is difficult to map out,” he said. “There are a lot of moving parts.”
LaBar, however, said the problems faced by truckers at marine terminals were present long before the coronavirus disease 2019 (COVID-19) and the explosive recovery this summer, and will persist into next year if something isn’t done quickly to improve communication among all of the supply chain partners, beginning with the ocean carriers.
LaBar noted that the Port of Los Angeles has invested millions of dollars in the Port Optimizer to enable the sharing of shipment information through the supply chain, and some of the terminals have invested in platforms that allow for advance sharing of shipment information, but participation by the carriers is still spotty.
“We need leadership from the two ports to make this happen. They need to do something bold to incentivize or compel dual transactions,” LaBar said.
TRAC Intermodal fully supports the sharing of shipment information in advance of vessel arrival, as it would make it easier for truckers to arrange dual transactions, resulting in benefits for the entire supply chain, Noel said.
“Collaboration and better shipment profile insight would be unbelievably valuable,” he said. “That’s a gap in the supply chain.”
Ag shippers slam carriers for refusing some export loads
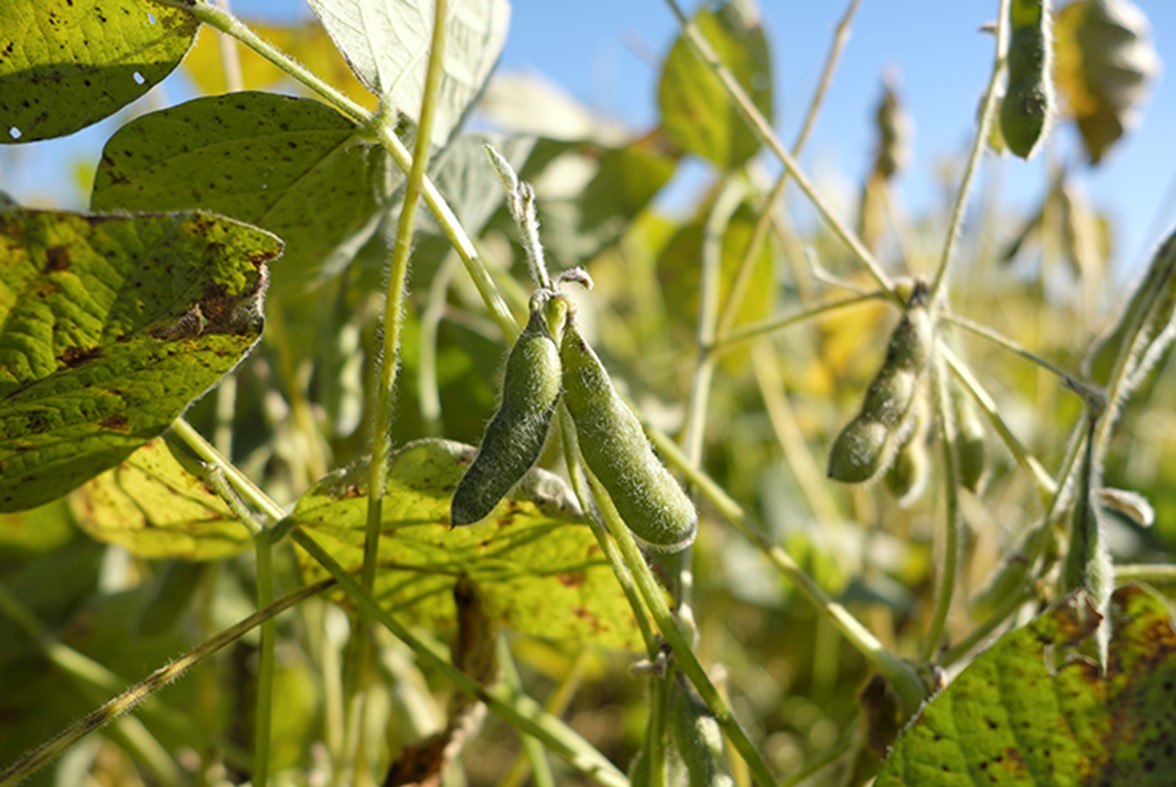
Soybean exporters decried a “bombshell” decision by Hapag-Lloyd to suspend liftings of some agricultural shipments in order to rush empty containers back to Asia where they are in short supply, and the exporters expressed concern that other carriers may take similar measures.
“Hapag-Lloyd has dropped a bombshell, informing exporters it is suspending overseas ag container shipments from North America, a decision that could cause major hardships within the entire US ag community,” the Specialty Soya and Grains Alliance said in a press release Friday.
However, Uffe Ostergaard, Hapag-Lloyd’s president, Americas, told JOC.com Friday the carrier did not take this decision lightly, and in fact is accepting some ag export shipments when they are generated in proximity to ports. For example, there are a number of transloading facilities near West Coast ports where grains are transferred from rail cars to marine containers.
Agricultural exports generated in the US interior will undoubtedly suffer, though, as they are denied access to the containers they need to ship products to destinations throughout Asia, especially if other carriers also reject shipments.
This is not the first time that trans-Pacific carriers have curtailed their liftings of US agricultural exports to Asia in order to expedite the shipment of the empty containers back to Asian load ports, said Mike Steenhoek, executive director of the Soybean Transportation Coalition.
“I see continued pressure on carriers to do this, and it comes at an awful time because this is our key export season,” Steenhoek said.
Suspension of ag export liftings may be spreading
Peter Friedmann, executive director of the Agriculture Transportation Coalition, said many exporters, including hay, resin, and forest product shippers, are already seeing other carriers restrict their export liftings. However, he said he has not seen any formal announcements from carriers other than Hapag-Lloyd.
“They have indicated they are suffering the same fate from various carriers who are choosing to ship containers empty rather than accepting export loads,” Friedmann said.
Ostergaard noted that Hapag-Lloyd is attempting to achieve a balance between its pressing need for more containers at Asian load ports and its commitment to US agriculture exporters to be a reliable carrier.
“We have to look at all parts of the business to make things run,” he said.
Trans-Pacific shipping lines and non-vessel-operating common carriers (NVOs) have told JOC.com that marine containers of all sizes are in short supply in Asia. Due to a surge of imports in North America and Europe, containers have backed up at distribution warehouses, and carriers have struggled to return the empties to ports for repositioning to Asia. Ostergaard said that because the import surge into the US is projected to continue at least until the Lunar New Year on Feb. 12, 2021, the container shortages in Asia will likely persist until then.
Reputation of US exports at stake?
Nevertheless, US agriculture shippers believe that carriers will continue to restrict export liftings primarily for economic reasons. They note that freight rates for US imports from Asia can be as much as eight times the export rates.
The spot rate for an eastbound shipment from Shanghai to the West Coast this week was $3,865 per FEU, according to the Shanghai Containerized Freight Index published in the JOC Shipping & Logistics Pricing Hub. The average westbound spot rate from Los Angeles to Shanghai was $518 per FEU.
Soybean shippers are being hit especially hard by carriers’ rejection of export loads. Although most US soybean exports, especially to China, move in bulk vessels, shipping soybeans in containers is crucial for secondary markets, Steenhoek said. According to the Soy Transportation Coalition, the top destinations for soybean exports in containers are Taiwan (28 percent), Indonesia (25 percent), China (11 percent), Thailand (10 percent), Malaysia (9 percent), Vietnam (5 percent), Japan (5 percent), and South Korea (2 percent).
“Ag shippers rely on containers to these markets, and now the rug is pulled out from under them,” Steenhoek said.
The Specialty Soya and Grains Alliance noted that all types of ag shipments could be harmed by carriers’ decisions to reject export loads. Farmers in the upper Midwest ship a variety of exports to Asia, including identity-preserved grains, peas, lentils, and other ag products for human consumption.
“This disrupts the food supply chain,” said Bob Sinner, president of SB&B Foods in North Dakota. “Companies in those countries rely on us for their food manufacturing. We’ve got our new crop harvested and we’re making significant and consistent bookings with carriers to get our products shipped quickly and as soon as possible,” Sinner said.
In a broader sense, US agriculture exporters say their reputation as a reliable shipper of all types of ag products is at stake. US products have always had an advantage over competitors in other agricultural export nations when it comes to their ability to fulfill commitments to overseas buyers and to ship their products in a timely, cost-effective manner due to the superior US transportation network. “Cost-effective, reliable transportation versus our competitors, especially in South America, is our main advantage,” Steenhoek said.
New Trans-Pacific capacity injections spark demand doubts
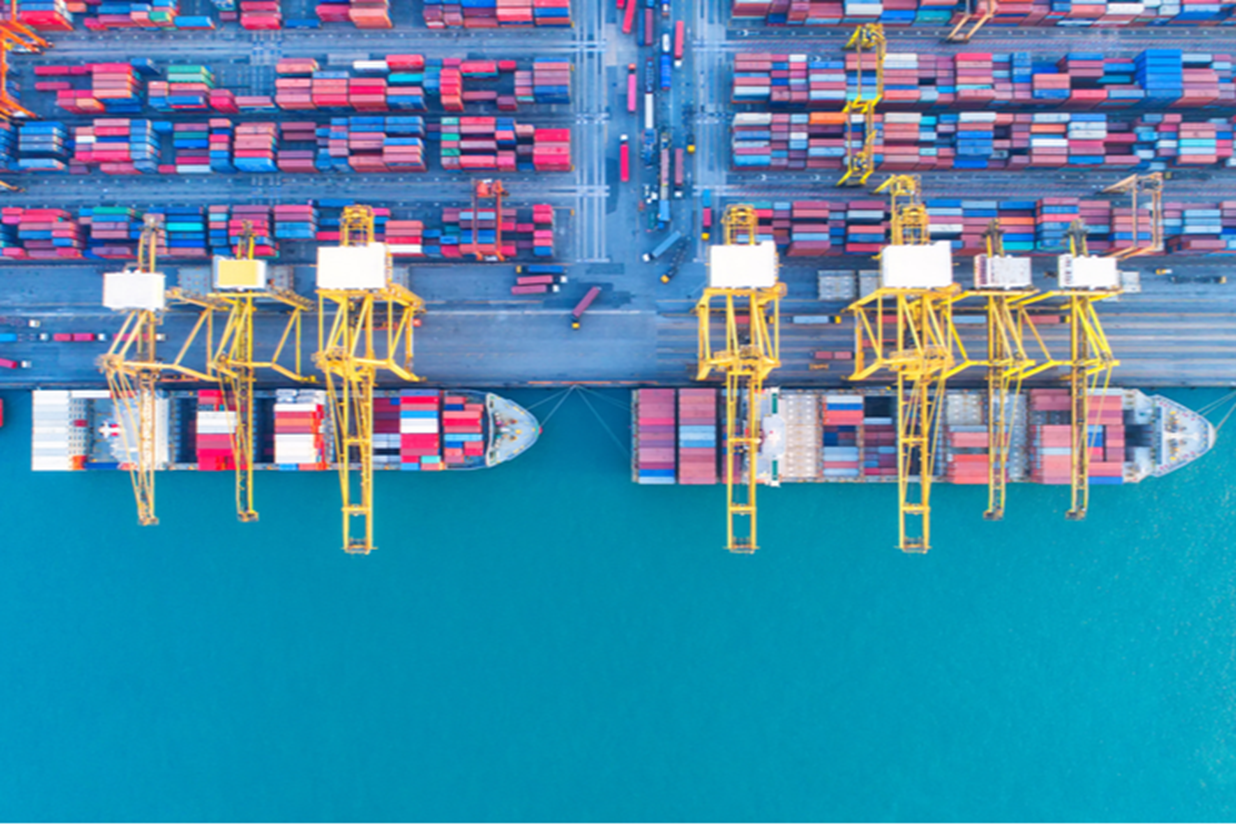
Industry observers expressed concern this week the US import surge that has resulted in a 20 percent year-over-year increase in capacity is not sustainable and could result in excess capacity in the eastbound trans-Pacific by early 2021.
Still, if carriers continue their year-long policy of managing capacity through a combination of blank sailings and extra-loader vessels, observers do not anticipate a significant decline in freight rates, at least not until the Lunar New Year lull in February.
In an editorial in the Sunday Spotlight entitled, “This Does Not Add Up,” CEO of Sea-Intelligence Maritime Analysis Alan Murphy said macroeconomic factors cited by The Conference Board will damage consumer spending in the coming months, including a projection of negative growth in US gross domestic product of 3.5 percent this calendar year, an historically high unemployment rate, and elevated savings rates.
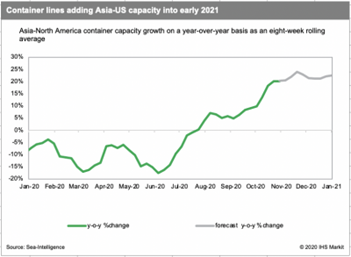
“It does not add up to a sustainable supply/demand equation, to see 20 percent-plus growth rates in demand in a time of market recession,” Murphy wrote. “While clearly, this is indeed currently possible in the short term, it is difficult to see a model whereby this is sustainable in the longer term.”
There are two primary schools of thought regarding the supply-demand balance in the Asia-North America trade. One line of thinking is that the trade will have excess capacity owing to recessionary forces and continued uncertainty over the coronavirus disease 2019 (COVID-19), but another theory is that e-commerce fulfillment and requirements for personal protective equipment (PPE) and other medical supplies could sustain demand well into the new year.
A third observation is that imports will sustain the increased capacity in services to the ports of Los Angeles and Long Beach, but carriers may have to adjust capacity on East Coast services if retailers continue to concentrate most of their shipments through Southern California.
Sunday Spotlight noted that carriers have consistently maintained a 20 percent year-over-year increase in capacity in the eastbound trans-Pacific. In some weeks capacity was 30 percent higher than last year. “And this is not only for the past weeks. It is also the level of capacity injection they are currently scheduling for the rest of 2020,” Murphy said.
Underlying economic factors are concerning
A carrier executive who requested anonymity told JOC.com Monday his company shares many of the same concerns outlined by Murphy. “The underlying consumer demand can’t continue the way it has been going,” the source said.
Paul Bingham, director of transportation consulting at JOC.com parent company IHS Markit, said the company’s latest report on US household consumption also shows a slowdown in consumer spending in the fourth quarter compared with the third quarter. That conclusion is based on a slowing economy, high unemployment numbers, and the failure of Congress to approve another stimulus plan similar to the initial stimulus that ended on July 30.
Although the shift in consumer spending from travel and services to the purchase of goods through online shopping is going to continue, unfavorable economic conditions should prevent any acceleration in spending habits, Bingham said.
On the other hand, the carrier executive said a recent survey of customers showed imports will remain strong, not necessarily owing to new demand for merchandise, but rather to restock inventory that had been depleted in the summer and early fall.
“They’re using November and December to catch up,” the source said. “We’re still getting calls from multiple customers looking for space.”
Increased capacity on Pacific Southwest services is possible
Although carriers do not appear to be considering reducing capacity deployment now, they are looking ahead to next spring to adjust capacity to the two coasts when they will set their new deployments for the year, the carrier executive said. If demand for e-commerce fulfillment, technology products, exercise equipment, bicycles, and PPE remain at current levels, and time-to-market considerations are still a main determiner of routing, carriers may increase vessel sizes on their Pacific Southwest services without doing so on the all-water services to the East Coast, he said.
A non-vessel-operating common carrier (NVO) who is a former carrier executive said shipping lines have always been willing to adjust capacity based upon individual trade lanes, so if import volumes remain strongest on the Pacific Southwest services, that is where carriers will devote more assets.
Bingham added that if airlines are not able to increase their trans-Pacific flights, which significantly reduces airplane belly space, importers of time-sensitive shipments will continue to patronize expedited services that charge premium rates for guarantees of equipment availability, priority loading at Asian ports, and priority discharge in Los Angeles-Long Beach. Most of the expedited services are deployed to Southern California.
If demand softens on other routes, carriers can be expected to manage capacity as they have done most of this year, Bingham said.
“Carriers have been amazing in maintaining discipline,” he said. “They’re not going back to a rate-destruction environment.”
Intra-Asia container rates surge on box, vessel crunch
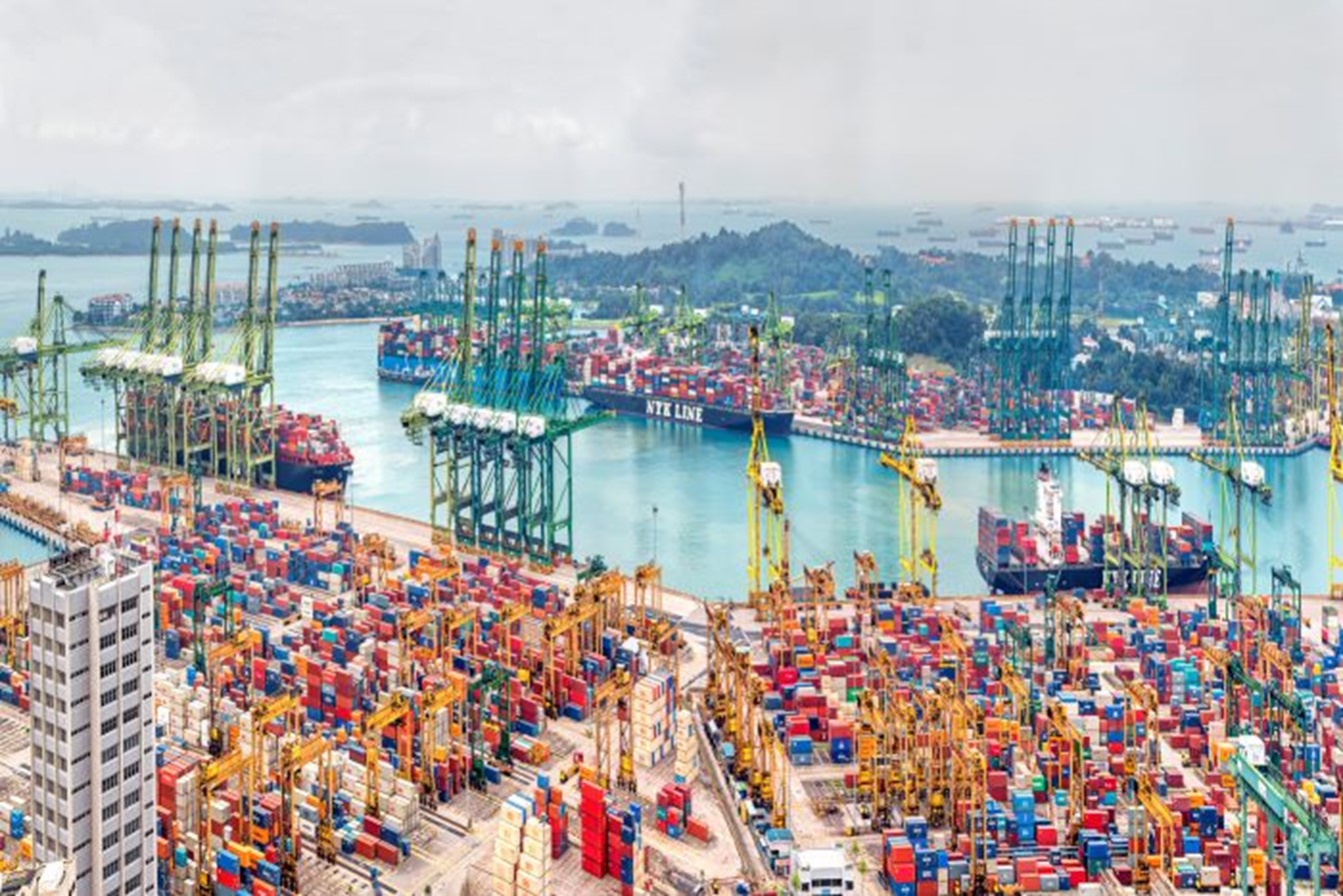
Freight rates on some intra-Asia services have soared to five-year highs in the last few weeks amid a capacity crunch, carriers and shippers said. The tightness in supply has mainly been caused by the global container shortage, carriers redeploying boxes and ships to main line services, and a regional economic recovery, executives added.
The rebound and resurgence of box volumes has encouraged carriers including Wan Hai Lines, Gold Star Line, Ocean Network Express, and OOCL to launch a raft of new services, sources said.
“Market rates for destinations in Vietnam, Thailand, and Malaysia are now the highest for five years,” Danny Hoffmann, managing director of Hong Kong headquartered Gold Star Line, told JOC.com. “Carriers are assigning containers and vessels to the long-haul trades as a top priority. With the trans-Pacific, Africa, and Australia markets booming from the second half of 2020, most carriers have started to void intra-Asia sailings, pulling vessels to put them as extra loaders on these trades. As a result, market capacity has been squeezed.”
Gold Star Line is the intra-Asia subsidiary of Israel’s Zim Integrated Shipping Services.
Detailing the rate increases, Chuah Seow Yong, general manager of the liner division at Singapore’s Pacific International Lines, told JOC.com that market rates for a 20-foot container from China to Vietnam and Thailand had climbed from $100 at the beginning of September to $450 to $500 in the second half of October.
Freight rates for a 40-foot box have surged from $200 in early September to $1,000 to $1,200 last week, Chuah said.
Rates are expected to rise further after OOCL, the Hong Kong-headquartered subsidiary of China’s Cosco Shipping Lines, announced rate increases on Thursday of between $150 to $300 for 20-foot, 40-foot, and 40-foot high cube containers from Hong Kong and south China to countries including Vietnam, Thailand, the Philippines, and Singapore from November 16.
OOCL will also increase rates by $50 to $100 for containers to east and north Asia, including Japan and South Korea.
The carrier reported that average revenue per TEU on its intra-Asia and Australasia trades rose to $653 in the third quarter this year compared with $630 in the third quarter last year. “The main reason for the surge in rates is the serious shortage of equipment in China,” Chuah said.
OOCL and regional carrier SITC both reported an increase in intra-Asia liftings last week. The stellar rates are a significant recovery from the beginning of the year when carriers were offering shippers rates as low as $1 per TEU rather than pay repositioning costs for empty containers from China to Vietnam and Thailand.
“In the early part of this year — actually it started in late 2019 — there was an oversupply of vessel capacity from China due to new services and slow demand. As a result, market rates did indeed crash to $1 per TEU at one stage. It was for only these two countries as direct services competed with regional and feeder services,” Chuah said.
His comments were echoed by Peter Sundara, vice president Global Ocean Product/Global Freight Management at Hong Kong-headquartered LF Logistics. “Rates have risen mainly on the back of a lack of 40-foot containers and a capacity crunch caused by blank sailings,” Sundara said.
LF Logistics is part of the Hong Kong-headquartered Li & Fung manufacturing and trading group.
Sundara said the situation has been exacerbated by main line carriers redeploying containers and vessels to the main trans-Pacific and Asia-Europe trades.
“The East-West trades are better paying in terms of yield management so mainline carriers will naturally prioritize 40-foot boxes for these trades compared with intra-Asia services,” he said.
Confirming Chuah’s comments of rates of $1 per TEU in January, Sundara said that while only a nominal amount, it made shippers liable for terminal handling charges and surcharges.
Those charges amount to about $265 per 20-foot box and $455 per 40-foot container on the China-Thailand route.
Lars Jensen, CEO and partner of SeaIntelligence Consulting, said in a LinkedIn post on Friday that the tight market was “also impacting some of the intra-Asia trades monitored by the Shanghai Containerized Freight Index (SCFI).” “Rates from Shanghai to Singapore have increased sharply from $135 per TEU just three weeks ago to now $254 per TEU – an 88 percent increase,” he said.
Weather a factor
Weather delays and port congestion in Asia, particularly in Busan and Ningbo, have also worsened the box shortage, with ONE reporting delays of a few days to up to 10 to 14 days on some services even as it omits calls at ports including Shanghai and Singapore to restore service reliability.
“Most services are facing serious delays due to the weather, which also results in congestion in terminals,” Gold Star’s Hoffmann said. Sundara said slot costs are also higher now, which has fueled the rate increase.
Executives said the equipment shortages coincide with a recovery in regional economies and the shift of production to other regional countries due to the China-US trade spat. This has seen containerized cargoes of raw materials, for example, being transported from China to the Indian subcontinent, especially Bangladesh, Sundara said. “Due to the surge in e-commerce and increased spending power by middle-income families, especially in countries such as Vietnam, Thailand, and Indonesia we’ve seen a cargo surge from China to South East Asia,” he added.
“We are also witnessing some customers using Vietnam as a distribution center for cargoes from Bangladesh and southeast Asia to China. This not only creates opportunities to increase intra-Asia volume, but also business for logistics providers,” he explained. “We will continue to see a surge in volumes through 2021 as suppliers source within Asia and consumers continue to import from China and southeast Asia.”
New, expanding services
It is against this background that carriers are launching new and expanding existing intra-Asia services. These include Thailand’s Regional Container Lines (RCL), which has teamed up with Gold Star Line to launch a Port Klang-Singapore-Ho Chi Minh shuttle service.
“With customers relocating their supply chains to southeast Asia and Vietnam in particular, both our customer owned- and shipper owned-container customers have requested us to improve our sailing frequency and connectivity between Ho Chi Minh, Singapore, and Port Klang,” an RCL spokesperson said. Gold Star Line’s Hoffmann told JOC.com, “We are always looking for the opportunity to expand our network. We started five new intra-Asia services in 2020 and expect to launch several more next year.”
Gold Star Line will launch a weekly China-Australia service from November 2. Taiwan’s Wan Hai Lines is launching a raft of new services including its Straits-Bangladesh Express Service with Singapore’s X-Press Feeders between Singapore, Malaysia, and Bangladesh on November 3 with two 1,200 TEU vessels.
Wan Hai will also inaugurate a weekly south China-Indonesia-Malaysia service from November 14 using three 1,800 TEU box ships. This will be followed a day later by the start of its joint China-India VI service with Sinokor Merchant Marine, Heung-A Line, Interasia Lines, and Feedertech using six vessels of around 4,250 TEU.
Hong Kong-based TS Lines has teamed up with X-Press Feeders and South Korea’s KMTC to launch a China-India West Coast X-Press service connecting China, Singapore, Malaysia, western India, and Pakistan, with six ships of 4,200 to 5,000 TEU.
Main line carriers ONE, Mediterranean Shipping Co., and OOCL are also expanding intra-Asia routes, with ONE launching seven new services this year, MSC extending its Golden Horn service to Incheon and three ports in China, and OOCL starting its China-India Express 3 and the China Straits 1 and 2 (CSS1 and CSS2) services.
That comes as Fung Business Intelligence, the research arm of Li & Fung, sees positivity in several countries across the region including Vietnam, Bangladesh, and Pakistan with an expected rise in foreign sourcing and exports of goods including garments and footwear.
CMA CGM expands intermodal surcharge to LA-LB haulage
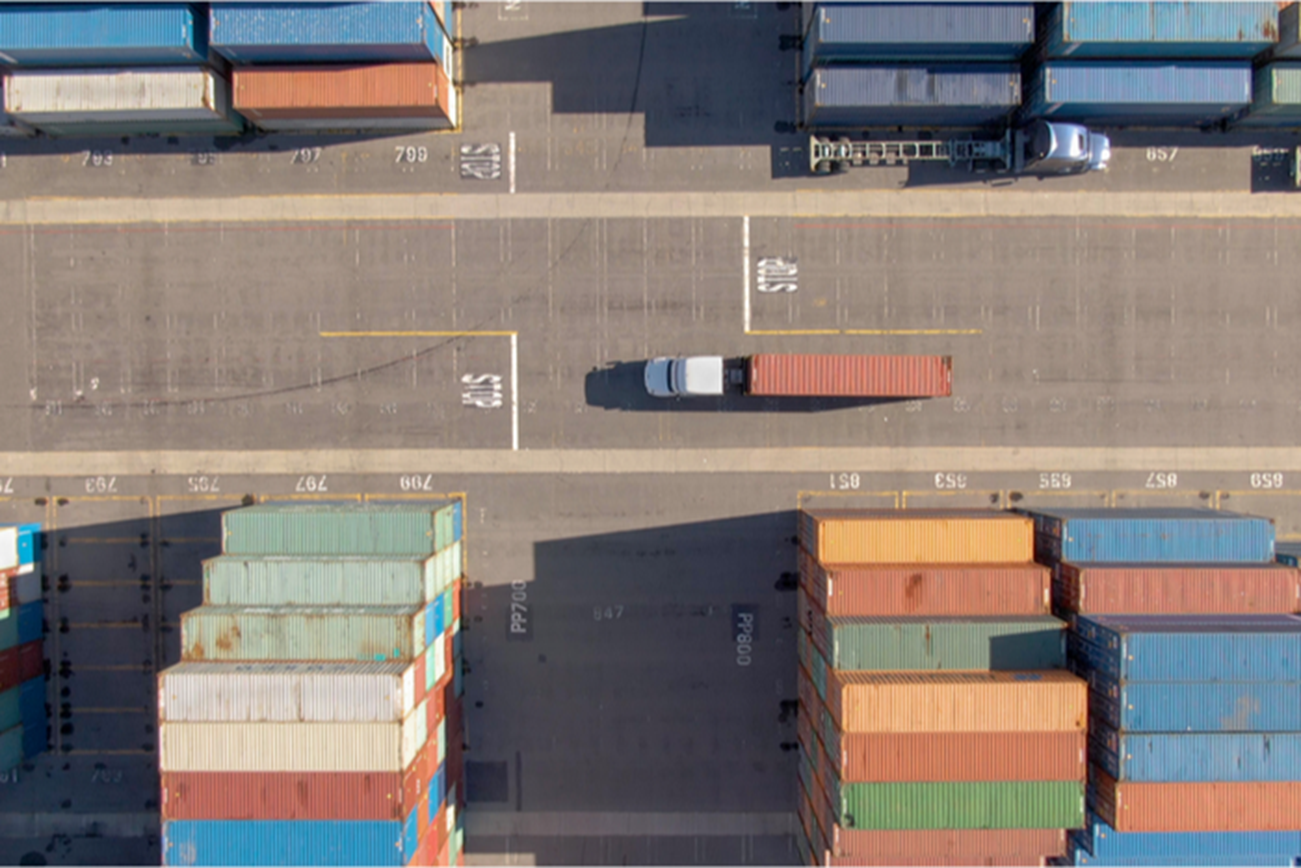
Citing congestion in Southern California, CMA CGM is expanding its $350 emergency intermodal surcharge beyond inland destinations to include all containers moved out of the Los Angeles-Long Beach port complex for local delivery and to area rail ramps.
In a customer notice Monday, the carrier said it will implement the emergency surcharge starting Nov. 30 and Dec. 2 at the ports of Los Angeles and Long Beach, respectively. CMA CGM said “the charge allows for managing escalating costs in order to continue to provide a proper level of service.”
The emergency intermodal surcharge currently only applies to containers originating from Southern California into nine major inland markets, including Chicago and Memphis. The expanded LA-LB surcharge applies to local truck delivery moved via carrier haulage, but such moves in which a shipper has designated a specific trucker are exempt from the fee. The emergency surcharge also applies to containers trucked from marine terminals and moved under merchant haulage to rail ramps outside the port in Southern California.
Under carrier haulage, the container line facilitates the trucking transportation from the marine terminal, whereas under merchant haulage, the shipper or consignee contracts a drayage provider to handle the truck move. CMA CGM’s move to expand the intermodal surcharge to Southern California reflects what some forwarders and drayage operators say is a worsening situation at the port complex as elevated Asia import volumes don’t let up. Chassis are in short supply, truckers struggle to get appointments to return empty containers, and marine terminals are overwhelmed. The tightening of US drayage capacity is most acute in Southern California, where retailers are funneling their imports to meet e-commerce demand and rebuild depleted inventories. With volumes elevated, port truckers are increasingly picking and choosing which marine terminal they’ll serve based on how long it will take them to pick up a load or return an empty or loaded container, said Brian Kempisty, founder of Port X Logistics, a trucking services provider at major US ports.
Unsurprisingly, drayage rates are rising. “You can't hire a driver for 30 bucks an hour right now,” Kempisty said, noting company drivers could be attracted by wages in the low $20s a year ago, but now it may take $35 per hour or more to get drivers in this current market.
Pandemic-disrupted markets put spotlight on forwarder value
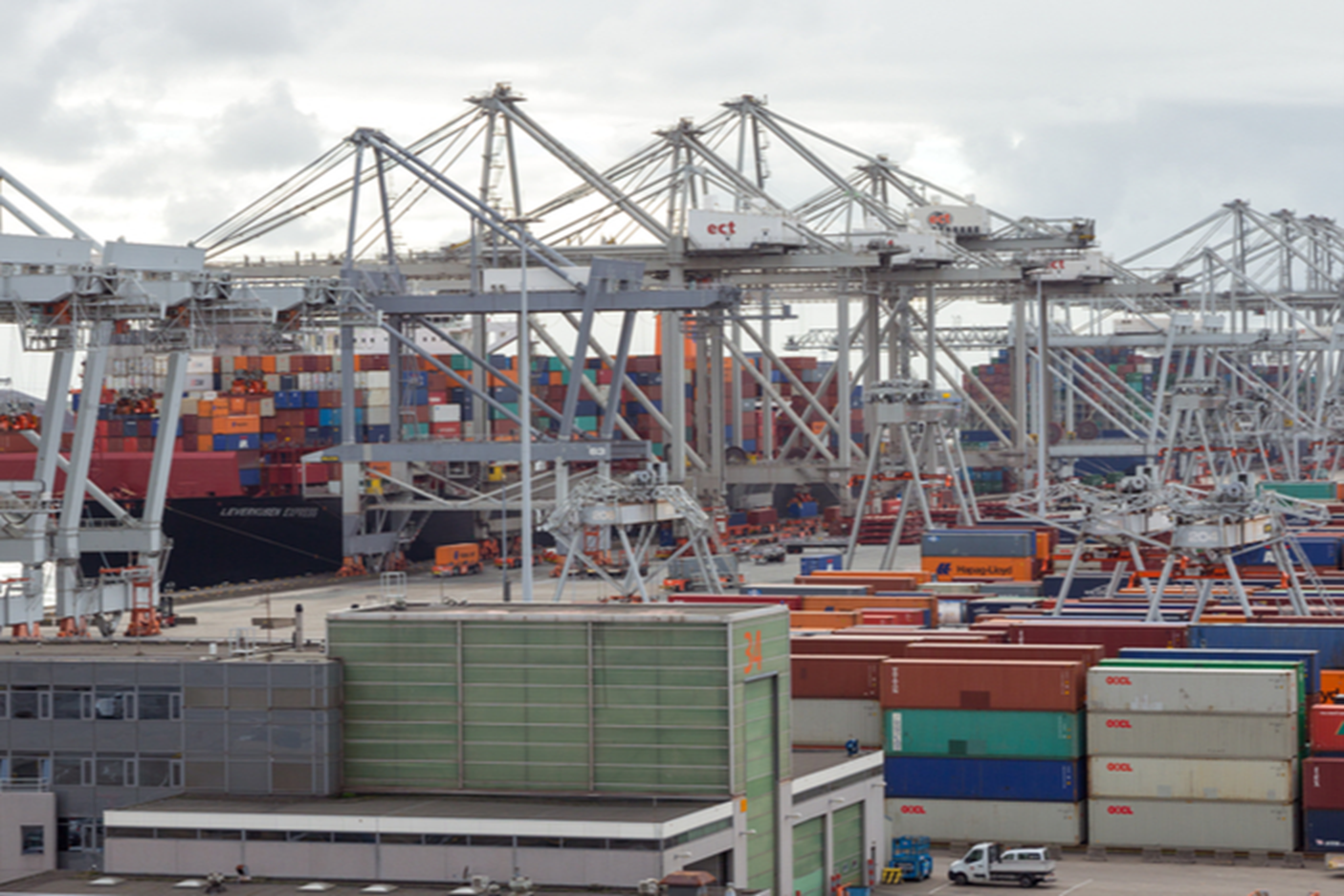
Securing container equipment and space on vessels out of Asia has become a priority for forwarders, with rates almost a secondary concern amid a chaotic freight market upended by the COVID-19 pandemic.
Forwarders are trying to leverage their global volume and years of building relationships with carriers to get customers’ containers on board ships leaving ports in Asia for North America and Europe, despite facing rising container equipment shortages, a lack of visibility in demand, and schedule reliability so poor in September that almost half the vessels calling at ports around the world were more than four days late, according to Sea-Intelligence Maritime Analysis.
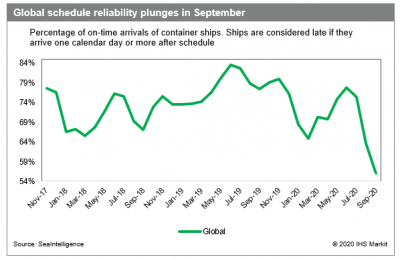
Click to enlarge
Dominique von Orelli, executive vice president and global head of ocean freight at DHL Global Forwarding, said BCOs and NVOs were dealing with a high volatility in the market, where agreements were not being met and both sailing schedules and allocations were changing constantly.
“The ocean freight market currently lacks much needed consistency and reliability, as some ocean carriers have chosen to be transactional,” he told JOC.com. “You can’t build a sustainable business model on the backs of other market participants and ultimately the customers.
“Given the unpredictability of some ocean carriers, it has become very difficult for NVOs to provide an adequate level of service to customers. Some ocean carriers actively manage capacity and yields by exploiting only the ad hoc market.”
Global lockdowns to slow the spread of the coronavirus disease 2019 (COVID-19), coupled with an unexpectedly strong recovery through the third quarter, have disrupted the entire global supply chain, said Michael Amri, global head of sea freight FCL at Hellmann Worldwide Logistics. He added that shippers and forwarders were now facing congestion at ports in China and Europe, full ships on the trans-Pacific and Asia-Europe trades, and huge imbalances building in container equipment.
“It is not only about rates right now; it is more about making sure the customers get the goods and keeping the supply chain alive,” Amri said. “On some trades, rates don’t even matter at the moment, you just try to get the cargo on a ship. Even if you pay sky-high rates and premiums, at least you get your box on board.”

Click to enlarge.
Thorsten Meincke, board member for air and ocean freight at DB Schenker, told JOC.com that it was up to forwarders and their relationships with carriers to ensure that cargo continued moving. But he warned that securing capacity in such a tight market would come at a price.
“If you treat your partners fairly and pay a decent rate, and if you ship above allocations, you need to pay premiums,” he said. “If you hammer a carrier on a super low rate and the market is currently twice what you are paying, then don’t be surprised if any excessive volume doesn’t run at this low rate level.”
As of Oct. 30, the average Asia–US West Coast spot container freight rate stood at $3,849 per FEU, up 142 percent from the same week in 2019, while the Asia–US East Coast rate was $4,641 per FEU, up 78 percent year over year, according to the Shanghai Containerized Freight Index (SCFI). The Asia–North Europe rate was up 61 percent year over year at $1,140 per TEU, while Asia-Mediterranean pricing increased 80 percent from the same week last year to $1,329 per TEU.
‘Abysmal’ carrier schedule reliability
Meincke said the availability of space on container ships out of Asia was supply and demand driven, but the bigger challenge facing service providers and shippers was adjusting to poor schedule reliability.
“There is massive disruption, congestion in ports, and weather,” he said. “We like to have everything in sync, but schedule reliability comes from the equipment problems, congestion, weather, volatility from customers, imbalanced trades, and larger ships with longer port handling.”
Sea-Intelligence Maritime Analysis data shows global schedule reliability falling to 56 percent in September from 77.4 percent in the same month last year, with the average delay per vessel rising to 4.75 days.
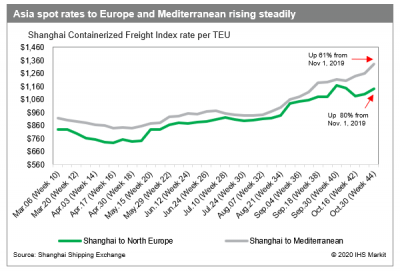
Click to enlarge.
“For our business model and the way we work, we need reliability,” Scott Phillips, supply chain and sourcing director of global shoes production and sourcing at footwear maker Ecco, said at the Global Liner Shipping conference Tuesday.
“Being rolled costs us money and reputation to our brand, so we need capacity load management to be sharper and carriers not just waiting for a guy with a bigger checkbook at the port to bump someone else off,” Phillips said. “This forced us into a partnership model with service providers, and we hope that having been partners with them for many years will stand us in good stead as the capacity constraints and the costs go up.”
Predictive supply chain analytics provider Portcast found the average schedule reliability from January through September fell 46 percent compared with last year, with a 64 percent increase in schedule delays for vessels arriving in European ports in the six months ended Sept. 30.
Jens Bjørn Andersen, CEO of forwarder DSV Panalpina, took a dim view of container carriers’ overall on-time performance in 2020. “The reliability is abysmal to say the least,” he told JOC.com in an interview last week. “If we had a similar level of service in our road product, for instance, we would have been out of business long ago. I would hope carriers will use their newly gained profitability in 2020 to invest in improving reliability, because it is leading to big constraints in the supply chain when you don’t know when your cargo is arriving.”
Andersen said DSV was one of the largest buyers of sea freight in the world, and was able to leverage that to secure slot allocations from carriers. “We are a large forwarder, so in most cases we get the space we need, and we have a very good relationship with all the carriers.”
Long list of reasons for vessel delays
Container imbalances have been very difficult for carriers to manage, especially considering the volatility of demand, which crashed during initial COVID-19 lockdowns only to come roaring back when they were lifted, according to Rolf Habben Jansen, CEO of Hapag-Lloyd. “When you look at the deployment of vessels in the trans-Pacific, the industry was able to react to [the increase in demand] quite swiftly,” he told the Global Liner Shipping conference.
“But when we look at equipment availability, with the volatile demand we ended up with the boxes in the wrong places,” he added. “No one expected the increase in exports from Asia to be so strong, and now all of us are fighting to get the boxes back.”
Carriers have told JOC.com the high level of supply chain disruption and poor on-time performance can be linked to a range of factors. No seasonality of demand in the second half has left carriers with no downtime to recover operations, while berth occupancy and terminal utilization in Asia and North America have been at all-time highs with extra loaders exacerbating the congestion. Added to this are weather delays, crew change issues related to the pandemic, positive COVID-19 tests that delayed ships in ports, rising dwell times, and delays in returning containers leading to equipment imbalances, with limited scope to increase the box fleet at short notice.
There was some sympathy from forwarders for the operational challenges container lines were facing.
“Carriers are investing billions into ships and equipment, and we expect them to constantly react to changes in the supply chain,” Meincke said. “Currently, the Asia outbound volume is booming like there is no tomorrow, but who would have predicted that in April or May? That instead of going on vacation, people would invest all that money saved in retail products.
“Now, everyone expects that the carriers ship everything,” he added. “There is nearly no ship available, so the argument that the carriers are artificially creating shortages is incorrect. There are just no ships available.”
Amri had the same view. “I don’t believe the carriers are [delivering poor service levels] on purpose,” he said. “COVID-19 has completely disrupted the supply chain and caused all the problems that come with it — capacity issues, space and equipment shortages, poor schedule reliability, and delays. While we can all be happy with the positive volume growth trend, that obviously comes with challenges as nothing is predictable and thus cannot be planned.”
Source: https://www.joc.com/